Product overview
The product is equipped with a thermal insulation device, which can heat the pump body through steam, hot water or hot oil to make the material flow better, prevent the material from solidifying in the pump cavity and the end face of the mechanical seal, avoid the overload of the pump and the damage of the mechanical seal during start-up operation, and realize the protection of the pump. It is suitable for working conditions where the viscosity of the material is greatly affected by temperature.
How it works
Hollysys rotary lobe pump consists of two rotors and pump body composed of multiple volumetric cavities, when the two rotors rotate synchronously in the opposite direction, the volumetric cavity periodically works - from small to large - fixed volume - from large to small to small to achieve the purpose of transporting fluid. The motor and reducer drive the pump spindle to rotate, and the electric energy is converted into the kinetic energy of the transported fluid medium through the pump, and the flow rate of the pump depends on the volume value of the working chamber and its change frequency per unit time, which has nothing to do with the discharge pressure (not theoretically and without considering the viscosity and fluidity of the material); The rotary lobe pump drives two synchronous counter-rotating rotors by the synchronous gear through the transmission shaft to form a fixed volumetric cavity between the two rotors and the pump cavity during the rotation process, which are: the volumetric cavity at the inlet changes from small to large to produce suction (vacuum) to suck in the material, and the volumetric cavity at the outlet changes from large to small, forming a conveying pressure to output the material. The volumetric chamber characteristics of the pump allow efficient passage of large, fragile soft solids, such as pulp-containing materials in food materials.
Application areas
• Daily chemicals: dish soap, laundry detergent, shower gel, skin cream, shampoo, hand soap, toothpaste, soap, washing powder slurry, daily chemical raw materials, etc.
• Fine chemicals: dyes, pigments, adhesives, silicone oils, leather oils, chemical additives, various colloids, various slurries, etc.
• Food: syrup, molasses, sugar paste, dairy, fruit juice, jelly, yogurt, honey, ice cream, filling, meat puree, sauce, bean paste, flour slurry, various sauces, hot pot base, soy protein, chocolate slurry, and other food fluid media.
• Papermaking: polyacrylamide (PAM), gelatinized starch, carboxybenzene/propylene latex, rosin, rosin gum, filler, dry strength agent, wet strength agent, sizing agent, retention and filter aid, defoamer, coating, water treatment chemicals, etc.
• Chemical fiber: viscose pulp porridge, PVA, vinylon slurry, acrylic slurry, amine slurry, polyurethane slices, polyester, polypropylene, artificial fiber, functional vitamins, etc.
• Medicine: all kinds of ointments, extracts, medicinal lotions, pill pastes, syrups, health products, pharmacies, etc.
• Coatings: paints, coatings, inks, insulating paints, resins, additives, organic solvents, etc.
Pump head construction
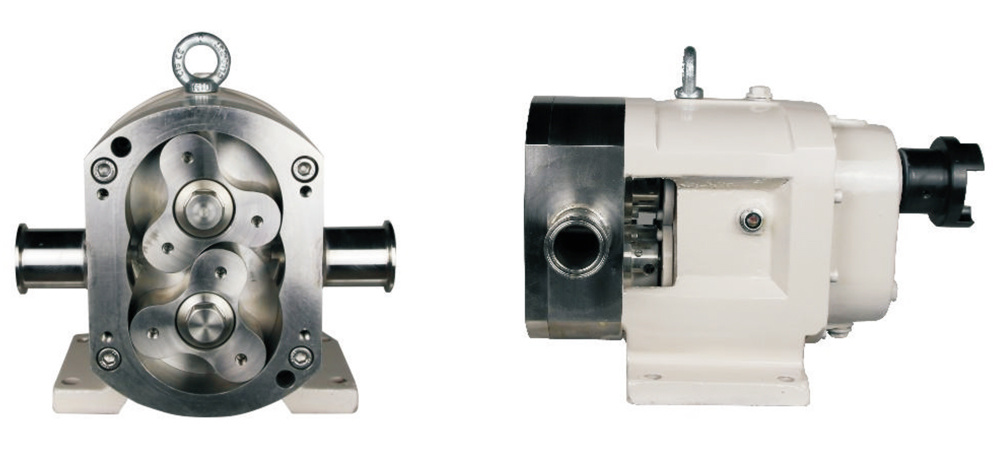
Rotary lobe pump working simulation diagram
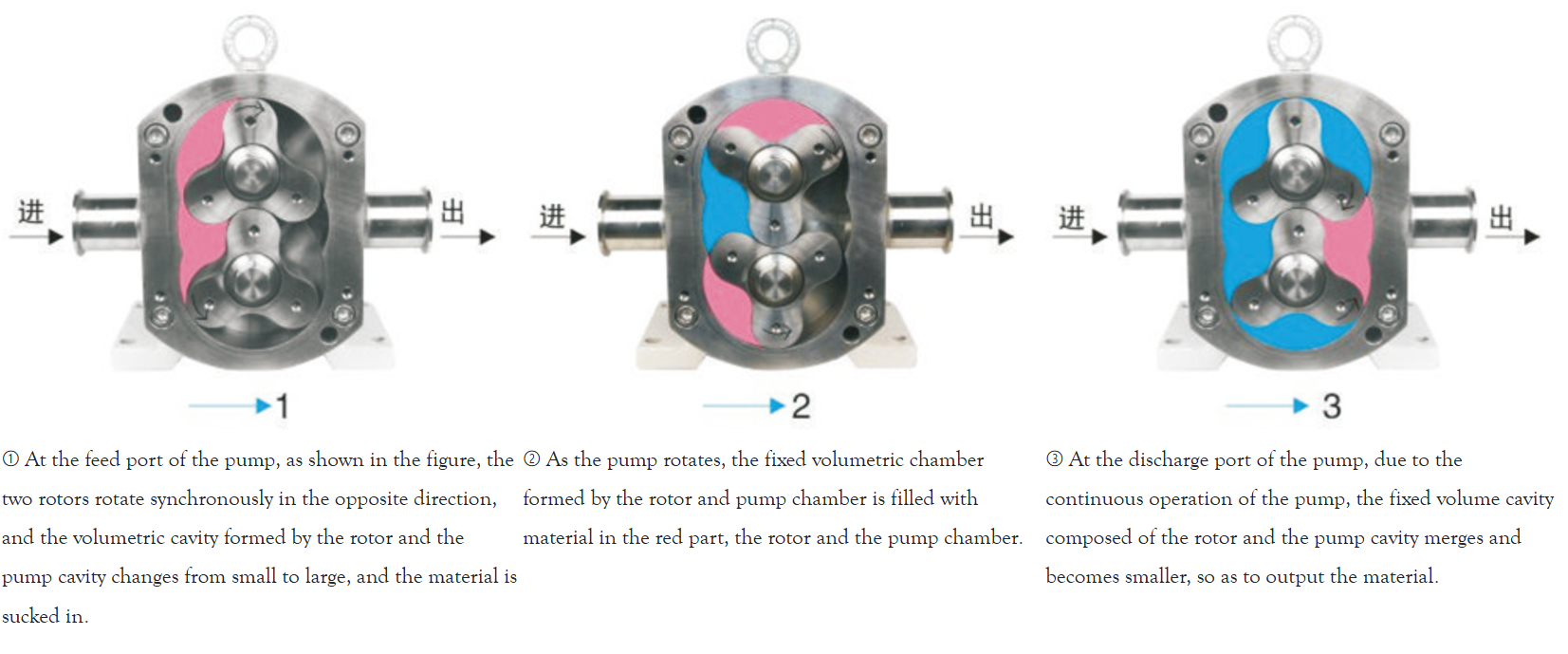
Introduction to the rotor
(1) Two-blade rotor: When the viscosity of the material is high (more than 8000cp) or the material concentration is high, the fluidity is poor, and the material contains soft small and medium-sized particles, this form of rotor is usually selected, for the above materials, the rotor can make the feeding smoother and can effectively protect the integrity of the particles.

(2) Three-blade rotor: dynamic balance, quietness, volumetric efficiency and other performance indicators are balanced, and the pump equipped with this type of rotor adapts to a wide range of conveyed materials, and is the most used rotor type in practical applications.
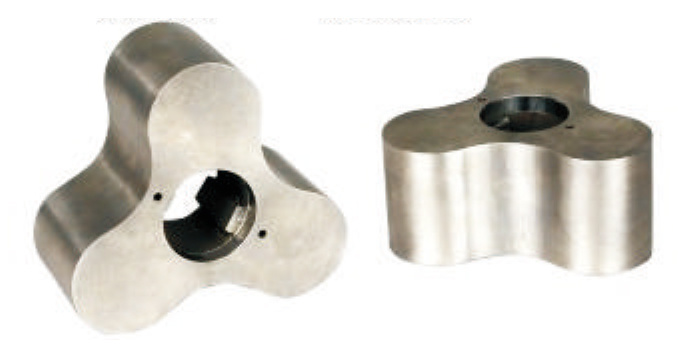
(3) Multi-blade rotor: This form of rotor is usually used in low flow rate and high pressure stability requirements, small flow conditions, according to the actual working conditions, usually choose 5-8 blade rotor, to meet the requirements of various special conveying processes.
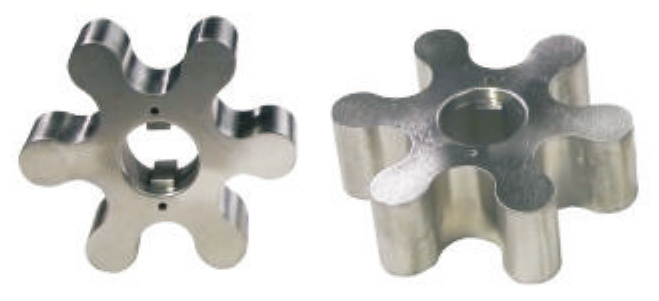
Introduction to sealing
Seal type: Mechanical seal
Seal configuration: general mechanical seal, water-cooled mechanical seal, oil-lubricated mechanical seal, water-cooled double-acting mechanical seal, cooling cycle pressure holding mechanical seal
Sealing end face material: silicon carbide-silicon carbide, silicon carbide-cemented carbide, cemented carbide-cemented carbide
Sealing O-ring material: fluoroelastomer, fluoroelastomer, perfluoroether, etc
Note: Special working conditions can be equipped with packing sealing.
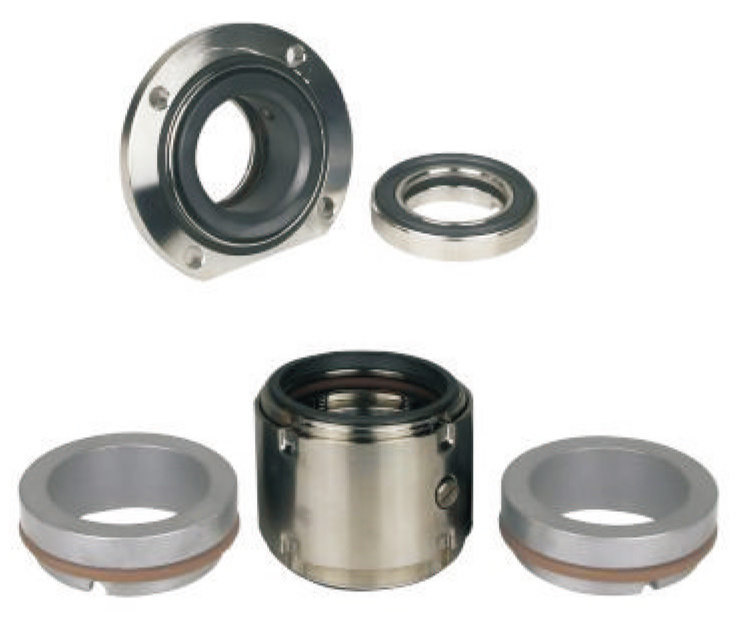