Paper Industry
Since its entry into the paper industry in 2004, Helsh-Tech's rotor pumps have been the earliest application promoted by our founder. They have greatly reduced manpower, increased production efficiency, facilitated operations, lowered costs, and simplified maintenance and repairs for paper enterprises. Highly recognized and widely used among served enterprises, Helsh-Tech is familiar with the production processes and working conditions of paper enterprises. Through continuous research and development as well as technological innovation, Helsh-Tech provides products and technical support for various material conveying requirements and has broadly addressed challenges posed by fluid media with high viscosity, strong corrosion and abrasiveness, and high solid content. These pumps are widely applied in polyacrylamide (PAM), starch sizing agents, liquid rosin, rosin size, pulp, dry strength agents, wet strength agents, sizing agents, retention and drainage aids, defoamers, water treatment chemicals, latex, coatings, and more.
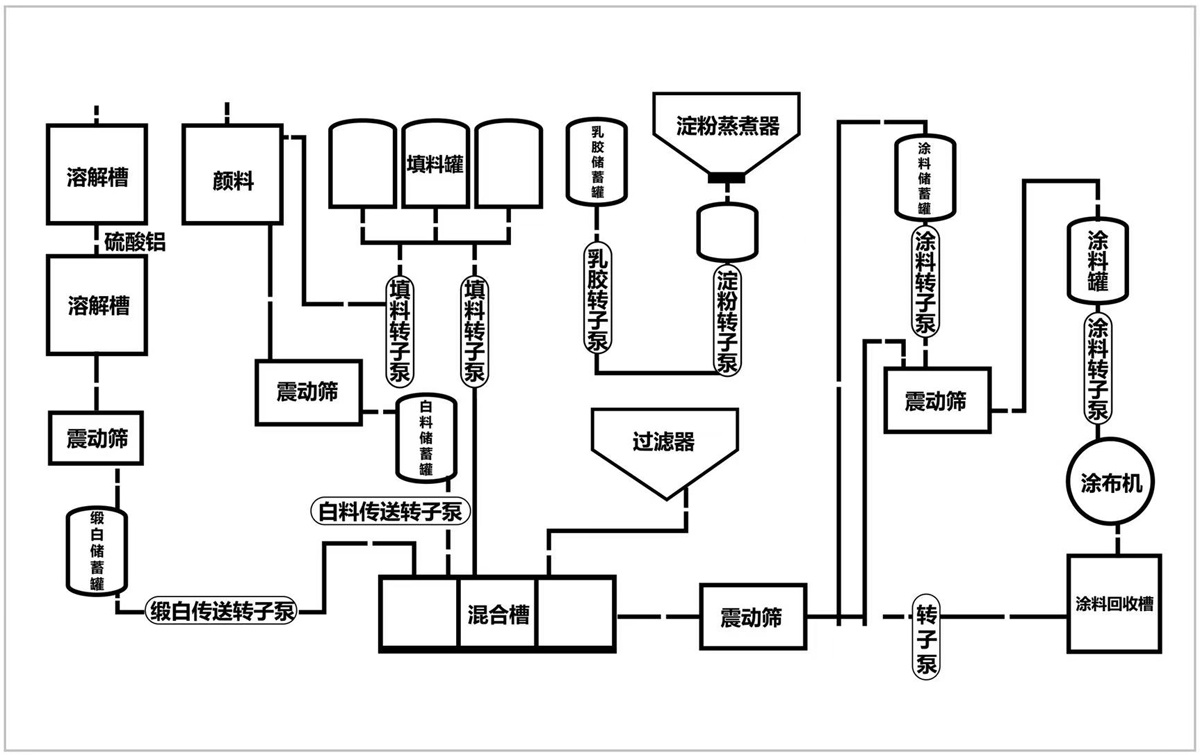
Engineering Cases
1.Helsh-Tech rotor pumps play different roles in paper production based on the materials they convey. They are suitable for wet strength agents (such as urea-formaldehyde resin and phenol-formaldehyde resin) to increase the wet strength of paper, retention aids (such as polyacrylamide, polyethylene oxide, and polyethyleneimine) to reduce the loss of fillers and fines during papermaking, and defoamers (such as silicone oil, turpentine oil, tridecanol, tributyl phosphate, pentanol, and octanol) to eliminate foam during papermaking. Water-repellent agents are primarily used in paper with high water resistance requirements (such as paraffin, metal soaps, glyoxal, melamine-formaldehyde resin, and dimethylaminoethyl acrylate).
2.Common media in the application of Helsh-Tech rotor pumps in coating preparation systems include kaolin, CaCO3, TiO2, talc, starch solutions, sizing agents, waxes, casein, proteins, formalin, alum, synthetic rubber, wet strength agents, defoamers, and bleaching agents.
3.The starch cooking and sizing feeding process involves high-temperature and high-viscosity conditions.
4.Due to the characteristics of various mixed chemical coating raw materials, the selection of the pump's flow passage components and mechanical seals is particularly important. It is necessary to be familiar with the characteristics of chemicals, auxiliaries, rosin, dry strength agents, wet strength agents, sizing agents, retention and drainage aids, and defoamers, and choose the best matching scheme. Moreover, the pH values and viscosities of various chemicals, their dosing amounts, and the complexity of working conditions vary. Comprehensive selection and matching are required. Helsh-Tech has provided robust technical solutions in this regard and received high recognition from enterprise operators.
5.Helsh-Tech rubber rotor pumps help paper enterprises address the treatment of production wastewater and sludge, aligning with the national emphasis on environmental protection. Wastewater from paper production contains hard impurities such as sand, coal residue, and pulp fibers, which can cause significant wear to conventional pumps. Helsh-Tech recommends using rubber rotor pumps to specifically address wastewater and sludge conditions, creating a good production environment. The rubber rotors of the rubber rotor pumps are made through a one-step molding process, which not only provides wear resistance but also effectively handles impurity particles with a diameter of up to 10 centimeters. The pumps operate smoothly, with lining plates added to the pump chamber to enhance the wear resistance of the flow passage components. Different materials are used for the mechanical seals to reduce the maintenance cost of vulnerable parts.